The Latest from Farm Industry News
Seven Springs Farm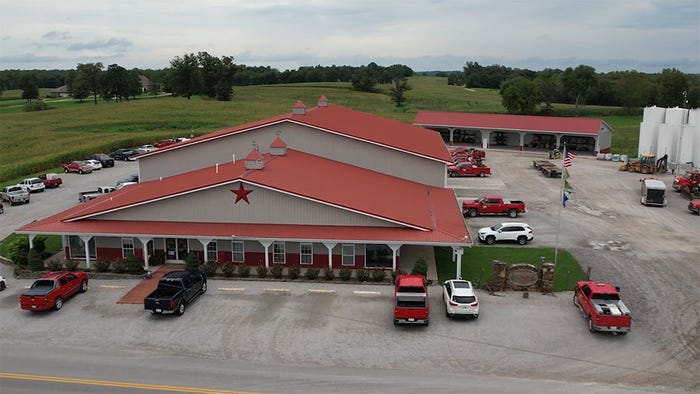
Sponsored Content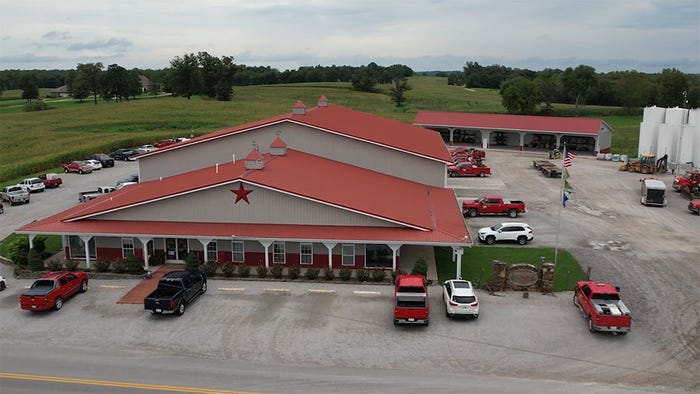
Data drives Seven Springs Farms' decisionsData drives Seven Springs Farms' decisions
Tech@Work: Host Willie Vogt is in Western Kentucky to learn how Seven Springs Farms uses data to have the efficiency of a factory on a family farm.
Market Overview
Contract | Last | Change | High | Low | Open | Last Trade |
---|---|---|---|---|---|---|
Jul 24 Corn | 451.5 | -0.5 | 453 | 450.25 | 451.75 | 02:42 PM |
Jul 24 Oats | 354.75 | +3.75 | 356.75 | 352.25 | 352.25 | 02:41 PM |
May 24 Class III Milk | 18.11 | -0.07 | 18.4 | 18.07 | 18.28 | 02:41 PM |
Jul 24 Soybean | 1178.25 | -1.5 | 1181 | 1172.5 | 1179 | 02:42 PM |
Aug 24 Feeder Cattle | 259.075 | +0.775 | 259.8 | 258.35 | 258.9 | 02:42 PM |
May 24 Ethanol Futures | 2.161 | unch — | 2.161 | 2.161 | 2.161 | 09:38 PM |

Copyright © 2019. All market data is provided by Barchart Solutions.
Futures: at least 10 minute delayed. Information is provided ‘as is’ and solely for informational purposes, not for trading purposes or advice.
To see all exchange delays and terms of use, please see disclaimer.
All Farm Industry News
Subscribe to receive top agriculture news
Be informed daily with these free e-newsletters